Process Flow Chart of Jute Spinning – Golden Fiber to Yarn
Jute Fiber
Process flow chart of jute spinning is described here. Among the bast fibers, jute is a lingo-cellulosic natural fiber derived from the skin of the plant’s stem. It is a composite fiber made of many ultimate fibers cemented together by lignin. Approximately 5-10 ultimate fibers are present in crosswise directions, and more than a thousand are in lengthwise directions in a single technical fiber.
As the cheapest natural fiber, it is regarded as the fiber of the future. Among plant fibers, jute is the most commonly used, consumed, produced, and available fiber extracted from stems of plants belonging to the genus vegetable. In Bengali, this plant is called Jhuto. As a natural fiber with a golden shine, it is referred to as the “Golden Fiber” of Bangladesh. The jute fiber is also called the bast fiber. We know that the fiber obtained from the plant’s bast layer is called bast fiber. As jute is obtained from the bast of the plant. That’s why jute fiber is called bast fiber.
Botanical name of jute
- Corchorus capsularis (White Jute)
- Corchorus Olitorius (Dark Jute)
These classes are further sub-divided into numerous grades denoting quality and other characteristics. They are:
- Hibiscus canabinus (Mesta Jute)
- Abutilong theophrasti (Chinese Jute)
- Hibiscus sabdariffa (Java Jute)
- Urena lobata (Congo Jute)
Flow chart of Jute Spinning

Now, I will describe the flow chart of jute spinning step by step.
1. Selection of Jute for Batch
The selection process involves opening raw jute bales and removing defects from the mora by experienced workers. Jute bales are available in two weights: 150kg and 180kg, with or without the top portion cut off. According to their end use, bales are sorted by Hessiean weft, Sacking wrap, Sacking weft, etc. The jute bales, after selection, are carried to the softening section by workers known as Gariwalas and Bajawalas. A batch of jute is made up of various types of jute to suit a particular class of yarns being spun.

2. Piecing Up:
Piecing up means opening a jute bale, separating the strong root from the jute, and making morah according to a specific weight (1-2 pounds).
3. Softening and lubrication:
Jute is a strong, difficult fiber that was used in the past for softening emulsions or spreading them. In general, morah jute is distributed evenly inwards of the softening or spreading machine, and the emulsion is applied at the open ends of the fiber. As a result of softening, jute morahs become pliable and soft. There are two methods of softening the jute; using a softening machine and using a suitable jute spreader.
Generally, emulsion plants with jute softener machines are used to lubricate and soften bark and gummy raw jute. An emulsion plant consists of a gear pump, motor, vat, jet sprayer, nozzles, an emulsion tank, and a jacket. Through this softening process, jute becomes pliable and soft, allowing it to be carded easily. An emulsion is an intimate mixture of two immiscible liquids where one is dispersed in small globules on the other, and the addition of a third substance brings stability. A standard emulsion consists of water 79.5%, Mineral oil 20%, and an emulsifier 0.5%.

4. Conditioning or pilling:
Conditioning or piling is the resting stage, where jute is applied after water and oil are applied. Using low-grade batching allows the barky root material to soften before passing on the cards, thus extending its lifespan. The main function of a pile breaker is to break down piles and feed them into carding machines. Pilemen carries softener machine output material to the pile placed by bile. When piling takes place, moisture penetrates the Fiber, and a “Thermo fillic” action occurs, softening the hard roots. After nearly 24 hours of piling, pile breakers transport the material to the carding machine.
Objects of pilling:
- To soften and split up of jute fiber.
- To loosen the fiber.
- To convert the rooty material into spinnable fiber.
5. Jute Carding
The process of breaking down long jute reeds while passing through a high-speed pin roller to form an entangled mass and delivering it as uniform-weight ribbons are called jute carding.
Objects of carding:
- To produce long continuous jute fiber from the general stage for keeping them nearly and separately.
- To straighten and parallel the fiber.
- Remove the dart, leaves, broken parts, and tiny fibers.
- To finish the different jute blending and mixing by different types of jute in carding.
- To paralyze the fiber separately.
There are two different carding sections:
- breaker carding
- finisher carding
Breaker Card:
After piling, soften jute is fed by hand to the Breaker carding machine in a suitable weight. In this machine, raw jute is transformed into jute slivers by the action of different rollers. Before feeding the material to the hand feed breaker carding machine, root cutting is necessary.
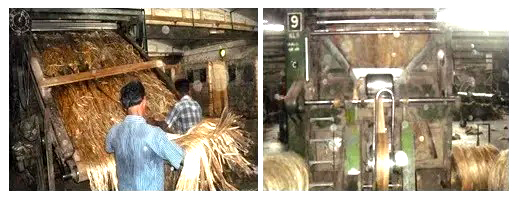
Finisher card:
Finisher carding machines make the sliver more uniform and regular in length and weight than Breaker carding machines. The Finisher carding machine has more pairs of rollers, staves, pinning arrangement, and speed than the Breaker carding machine. This machine feeds about 4 to 12 slivers obtained from the Breaker carding machine. After obtaining the material, the drawing section receives it
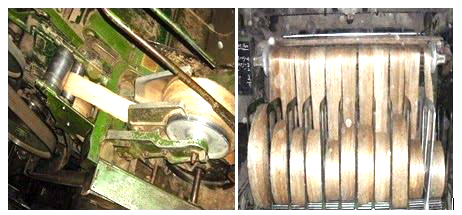
6. Jute Drawing:
A drawing process reduces a sliver’s width and thickness by mixing four to six slivers together. In general, there are three types of Drawing Frame machines. Typically, 3 drawing passages are used in Hessian mills and 2 in Sacking mills.
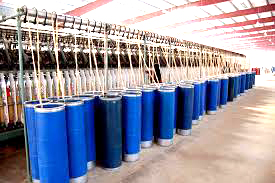
Objects of jute drawing frame:
- straightening of fibers in the sliver.
- Parallelization of fibers in the sliver.
- To reduce the weight per unit length of sliver.
- To reduce the thin and thick places in the sliver.
- To make the sliver spinnable.
As we know, jute fiber is hard. To make it soft, we used three types of drawing.
First Drawing:
In the first drawing frame machine, four slivers are fed from the finisher carding machine. First drawing frame machines are used for blending, equalizing slivers, and doubling two or more slivers, providing quality and color. This machine includes delivery rollers, pressing rollers, retaining rollers, faller screw sliders, check springs, back springs, and crimpling boxes.
Second Drawing:
The Second Drawing Frame uses six slivers and deliveries per head and obtains slivers from the First Drawing Frame. Second Drawing machine creates more uniform slivers and reduces the jute into a suitable size for third drawing.
Third Drawing:
The Third Drawing frame machine uses the sliver from the second drawing. As the Third Drawing machine is high speed, it makes the sliver more crimpled and suitable for spinning.
7. Jute spinning:
The spinning process produces yarn from sliver obtained from the third drawing. Jute spinning frame machine with slip draft zone produces quality yarns at high efficiency with auto-doffing facility.
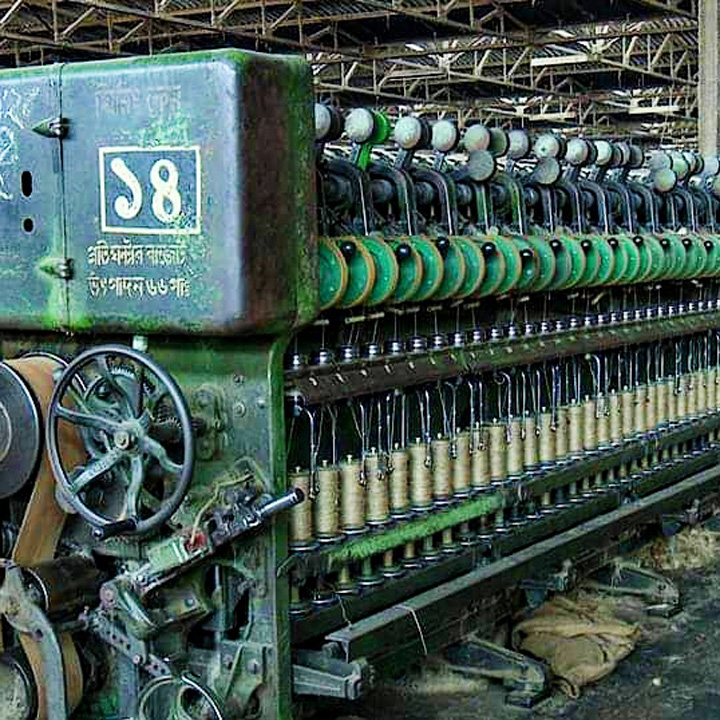
Objects of jute spinning:
- Drafting: the sliver speed to the machine is to reduce weight per unit length according to the count of the yarn by drafting.
- Twisting: the required amount of twist should be applied to the drafted material so that the component fibers of yarn in position to make a stronger yarn.
- Winding: twisted yarn is to be wound on a upright bobbin in a particular way and make easy to transfer from one place to another.
8. Winding:
The winding process produces spools and cops of yarn used in beaming and weaving.
There are two types of winding :
- Spool Winding
- Cop Winding
Spool Winding:
Spool winding produces longitudinal yarn for the warp. In a spool winding machine, there are a number of spindles. The number of spindles per machine varies widely from one manufacturer to another. The productivity of spool winding is determined by the spindle’s surface speed and the utilisation of the machine.The spool winding machine uses bobbins with smaller yarn lengths. The yarn was wound into bigger packages known as ‘spools’ by this machine. Spools of yarn are used to create warp portions used during weaving interleaving.
Cope Winding:
Cop Winding machines obtain yarns from spinning machines. The spinning bobbins are placed on a suitable pin on top of the cop machine, and the tension of the yarn is maintained with a small leaver. Bobbin yarn is converted into a hollow cylindrical package known as a cop. Transverse threads are interlaced using cops during weaving. Generally, cop winding machines have 120 spindles.
References
- Hossain, M. S. (2014). Introduction to Textile Engineering. Dhaka: Books Fair Publications.
- Kadolph, S. J. (2009). Textiles. New Delhi: Dorling Kindersley.
- Siddique, D. H. (n.d.). Natural Fibers. Dhaka.